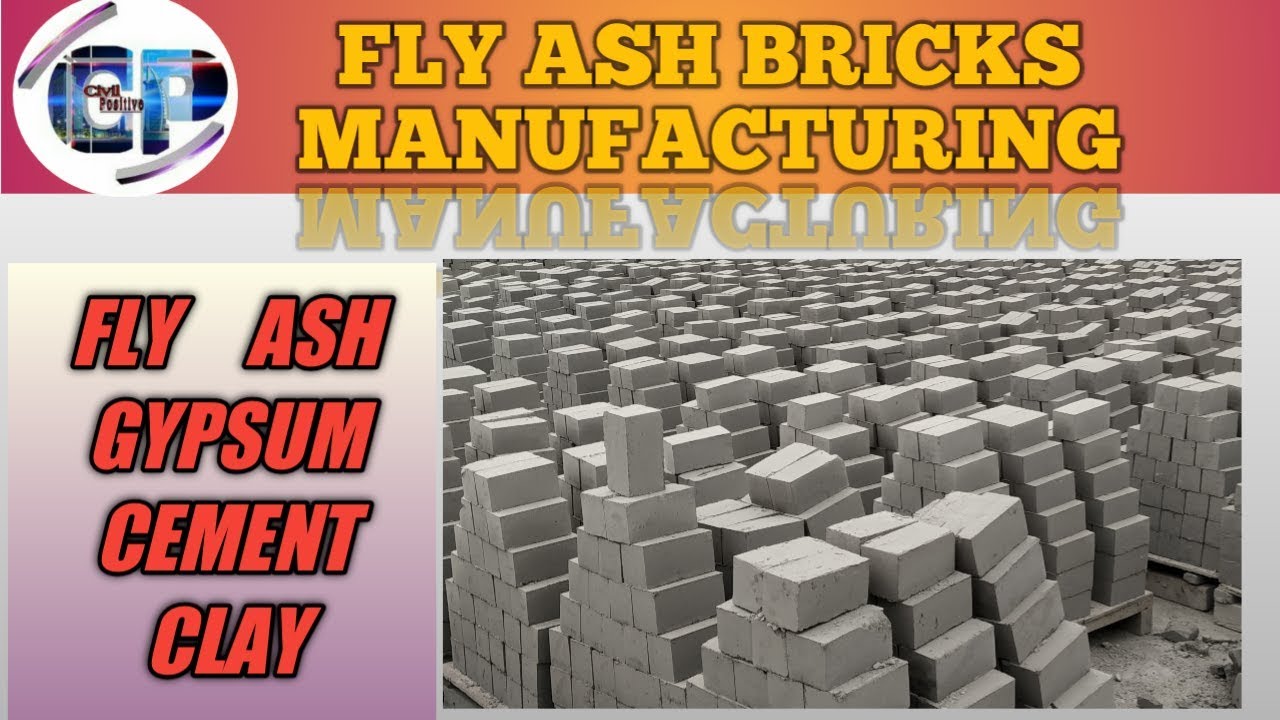
#FLYASH
#BRICKS
#CivilPositive
Fly ash brick (FAB) is a #building material, specifically masonry units, containing class C or class F fly ash and water. Compressed at 28 MPa (272 atm) and cured for 24 hours in a 66 °C steam bath, then toughened with an air entrainment agent, the bricks last for more than 100 freeze-thaw cycles. Owing to the high concentration of calcium oxide in class C fly ash, the brick is described as "self-cementing". The manufacturing method saves energy, reduces mercury pollution, and costs 20% less than traditional clay brick manufacturing.
The #raw materials for Fly Ash Bricks are:
--------------------
Material Mass
Fly ash 60%
Sand/Stone dust 30 %
Ordinary Portland Cement/
(Lime+Gypsum) 10%
Total formula of material 100%
The #strength of #fly ash #brick manufactured with the above compositions is ranges between 7.5 MPa and 10 MPa. Fly ash bricks are lighter and stronger than clay bricks.
Main #ingredients include fly ash, #water, #quicklime or #lime sludge, cement, aluminum powder and gypsum. Auto claving increases the hardness of the block by promoting quick curing of the cement. Gypsum acts as a long term strength gainer. The chemical reaction due to the aluminum paste provides AAC its distinct porous structure, lightness, and insulating properties. The aforementioned properties set it apart from other lightweight concrete materials. The finished product is a lighter block, less than 40% the weight of conventional Bricks, while providing the similar strengths. The specific gravity stays around 0.6 to 0.65. Using these blocks in buildings reduces the dead load, allowing one to save around 30 to 35% of #structural steel, and concrete.
Commercial processes fall into two categories; the lime route, and the #cement (OPC) route where the latter is used as a source of lime. In the #lime route, the composition is fly ash (50%), slaked lime (30%), and anhydrous gypsum (20%), to which 3 to 4 times of stone dust, sand or any inert filler material can be added. In the cement route, the composition is fly ash(76%), OPC (20%), and anhydrite (4%), to which 3 to 4 times of filler material can be added.
The following properties of fly ash affect the strength and look of fly ash bricks.
Loss on Ignition (LOI): fly ash loses weight when it burns at about 1000 °C due to presence of carbon and water. The weight loss happens due to carbon combustion and #moisture #evaporation is called "Loss on Ignition(LOI)". This is expressed as percentage. The lower the loss of Ignition, the better will be fly ash. As per BIS it should not be more than 5%.[citation needed]
Fineness: fine fly ash has more surface area available to react with lime. This increases activity, which contributes to the strength of fly ash bricks. As per BIS it should not be more than 320 m2/kg.
Calcium (CaO) content: the #pozzolanic reactivity of fly ash is more in high calcium fly ash. The greater the pozzolanic activity leads to higher the strength of fly ash brick. As per ASTM C618 fly ash is classified into two types: Class C contains more than 10% lime and Class F fly ash contains less than 10% lime.[3]
#Advantages
It reduces #dead load on structures due to light weight (2.6 kg, dimension: 230 mm X 110 mm X 70 mm).
Same number of bricks will cover more area than clay bricks
#High fire Insulation
Due to high strength, practically no breakage during transport and use.
Due to uniform size of bricks mortar required for joints and plaster reduces almost by 50%[citation needed].
Due to lower water penetration seepage of water through bricks is considerably reduced.
Gypsum plaster can be directly applied on these bricks without a backing coat of lime plaster.
These bricks do not require soaking in water for 24 hours. Sprinkling of water before use is enough.
#Disadvantages
Mechanical strength is low, but this can be rectified by adding marble waste or mortar between blocks.
Limitation of size. Only modular size can be produced. Large size will have more breakages.
It is only good for the places like subtropical area or area where climate is warm because it doesn't absorb heat. But during cold it is not helpful.
#fly ash bricks #manufacturing #process.
1.Land Requirement
2.Factory Location
3.Availability of Water
4.Environmental Issues
5.Total Project worth
6.Cement Manufacturers
7.Labor Availability
8.Profit Factor
9.Fly ash availability
10.Machinery Purchase
11.Composition of Fly Ash Bricks
---------------------------------------
The important compositions of fly ash bricks are:
#Fly ash
#Cement
#Sand
#Water
----++++++-------------🏗️🏗️
Any queries related to this video's contact me by email
-----------------------
'mdahedalam549@gmail.com'
Please subscribe our channel & share to other person....
#stayhome.
#staysafe
0 Comments